—方案實績— |
|
|
|
|
|
|
近年產業景氣變幻莫測,本團隊所輔導之產業客戶雖多經歷數十年景氣循環,企業主仍感壓力倍增,深知務求本業穩健經營,厚植研發與管理實力,提昇員工素質與能力,才可長可久。企業經營多年所蘊藏的智慧與時推移並在管理上不斷精進,是值得我們觀摩學習的對象。
全力盟 謹誌 |
|
※以下內容部份數據因涉及廠商營運資訊,換算後以百分比說明。 |
|
|
|
|
|
|
|
|
 |
產業別:車輛零組件業 |
|
導入/輔導效益: |
|
年營收規模:35億NTD
導入/輔導方案:模具e化管理平台 方案內容
|
|
◆產品開發時程平均縮短10%以上
◆共用模具相關文件查詢時間縮短50%以上
◆模具開發進度相關文件產出過程縮短50%以上 |
|
摘要: |
|
廠商為一專業之車輛零件OEM/ODM開發製造商(股票上市公司),由於為確保終端客戶產品上市期程的重要性;為加快量產時程,而使得廠商對關係著試量產進度關鍵之一的模具開發上,希冀透過一模具e化管理平台的導入,一方面能即時掌握模具的開發進度。二來為了集團全球三國七生產據點佈局,之間試產製程資訊無落差與透通性,以因應未來幾年的營運擴張計劃。
|
|
廠商在此模具e化管理平台上對於模具的開發設計與加工進度管理上,進行文檔、結構(模具BOM)、與模具工期的管理,使得開發部門、模具製造部門、品保部門、委外工程協力商,能在一共同平台上溝通保留開發過程間一直到售後客訴間的問題,追蹤開發進度。導入過程輔導手法上應用了資料結構化分析與資料屬性規劃有效的將模、治、檢具的工序、文檔、模具結構及開發進度做作一整合,以利資料與資訊能順利在同一平台上迅速流通。導入後廠商在縮短產品開發時程上有顯著的效益。
|
|
|
|
|
|
|
 |
|
|
|
|
 |
產業別:精密機械/整廠turnley輸出設備業 |
|
導入/輔導效益: |
|
年營收規模:約16億NTD
導入/輔導方案:
精密機械研發管理優化方案
|
|
◆縮短專案開發製造發包準備時間
◆提高訂單交機達交率
◆提高設變作業時效:
*設計變更處理週期平均縮短20%
*降低設計變更未結案平均件數30%
◆強化工廠管理績效:以整體性控管觀點出發規劃設變審查流程,使得導入後廠務主管能順利追蹤重要設變進度,進一步強化工廠管理績效。 |
|
摘要: |
|
廠商為一專業之機器開發製造商,由於接訂產業客戶之整廠生產線設備,因此大部分的機器都會依據不同需求進行設計及製造,因此如何有效迅速銜接從產品開發到零件發包間的過程,避免因設變流程中各單位間資訊不透明,導致發包作業延誤或圖面版本錯誤,導致延宕後續機台裝配、測試、交機時程。是廠商所關切的管理重點。
在此前提下,透過建立產品工程BOM與製造BOM間之轉換機制;使得工程BOM與製造BOM間能快速轉換規轉入到ERP進行零件發包與整機製造成本估算。另一方面利用設變作業e化工作流程,從設計變更需求提出、設變作業處理一直到設變通知各階段中之作業與流程: |
|
包括設變申請、審查與通知流程,工作流程中研發主管可線上簽審、加註意見;開發專案參與與相關人員(品保與採購)可參考設變圖面與相關文件與相互溝通;過程記錄被完整保留,設變零件發包進度可隨時follow up進行跟催,並查詢所有完整串連之設變資訊。
輔導過程中顧問透過將工程與製造BOM轉換原則模式化以及同步工程工作流程設計之手法,來建立機制與規劃流程,以達到廠商所關切的管理重點。在上線作業後廠商表示,在縮短專案開發製造發包準備時間、設變作業時效、訂單交機達交率上有著顯著的績效提昇。
|
|
|
|
|
|
|
 |
|
|
|
|
 |
產業別:精密機械/木工機器設備業 |
|
導入/輔導效益: |
|
導入/輔導方案:
精密機械研發管理優化方案
|
|
◆降低ISO 9001內稽準備作業費用
◆售服維修處理時間平均縮短了3~5天。
◆模夾治具維護費用與降低生產不良品等每年節省估計數十萬元。
◆每次調閱售服文件所需時間平均縮短10分鐘。每月均需調閱數百次。 |
|
摘要: |
|
客戶為一專業木工機器製造商,近年公司推行ISO制度並具體落實後,由於公司創立至今已滿五十年,發現研發過程中產出為數龐大的文件管理不易,不論在售服維修文件的調閱;ISO 9001稽查設計管制程序時,都已產生相當程度的困擾。因此公司計劃重新檢討流程,以研發部門為中心,將產品相關文件管理電子化。另外在模夾治具方面管理不佳,存在模具送修費用不符經濟價值;使用未依標準程序造成品質不良;未使用專用治具造成自主檢驗成效降低等等現象,公司希望能一併進行診斷。
在深入了解後,顧問診斷應優先以售服維修文件、設變作業表單、以及模夾治具資料透明化優先處理能有具體的效益,然而挑戰是如何將這些龐雜的資料在系統中串連;並讓人員日後能輕易調閱利用;另一方面人員編制上工作量並不低,為避免日後增加太多額外的工作負擔。 |
|
經與研發主管密切溝通後,雙管齊下採取文件架構規劃以及表單作業合理化,一來將設變作業相關資料、售服文件、以及模夾治具等文件,依其用途、欄位屬性、調閱時機以及和bom、圖面等資料,規劃出管理架構,使得文件在資訊系統中能輕鬆調閱,並彼此串連。二來將模夾治具相關表單與設變表單相關表單進行合理化後,使文件e化管理效率提高。
此案例特別之處在於廠商本已有PDM(產品資料管理系統),但以往公司對系統之應用僅在於產品圖面與BOM之管理。而此次所有的輔導方式與應用,顧問均在既有系統功能環境之限制下來進行規劃,在三個月間完成輔導後續追蹤下,廠商表示在輔導後才了解到在售服維修處理回應時效、ISO內稽作業費用、模夾治具維護費用原來還有許多改善空間。 |
|
|
|
|
 |
|
|
|
|
 |
產業別:手工具業 |
|
導入/輔導效益: |
|
導入/輔導方案:多生產據點生產管理方案
方案內容
|
|
◆接單允諾交期天數縮短30~40%。
◆導入後各產品線半成品平均庫存水準降低10~20%。 |
|
摘要: |
|
廠商為一專業之手工具ODM/OBM開發製造商,開發製造經驗近三十年。產品屢獲國內外設計獎項。近年產品線不斷擴充,公司半成品庫存卻因此與日俱增。而為滿足客戶彈性需求,訂單內容頻繁變動也造成產銷的不穩定。另一方面海外生產與台灣工廠之間生產步調的協調不一致與產能的分配也困擾著廠商。為因應此多生產據點與日益增加的產品線所衍生之諸多問題。廠商希望在生產管理上能有一具體可數據與模式化之方法來改變現狀,讓生產能因應訂單銷售之需,但仍能保有經營上的穩健與避免產能利用率的低落。
|
|
在進一步深入了解後,歸納出廠商產銷上的現況有已接訂單之數量交期變動大、允諾交期長;海外生產據點預訂工期與實際生產常有落差;半成品生產計劃與庫存水準安全水位偏高等現象。
對此我們採取了建立交期協調機制、縮短接單允諾交期的方式;並運用料品編碼分階、製造BOM架構設計、以及ANPS新生產技術中的工程同步化概念等管理技術,讓廠商能充份利用ERP中的MRP模組與APS系統的運算效能來規劃半成品生產計劃。
在方案運行半年後,效益陸續顯現。不論在半成品庫存量的降低、數據精確度的提高;或對海外生產狀況的掌握等方面,廠商表示均有令人滿意的成果。 |
|
|
|
|
 |
|
|
|
|
 |
產業別:製鞋業 |
|
導入/輔導效益: |
|
導入/輔導方案:台商企業組織再造合理化方案 |
|
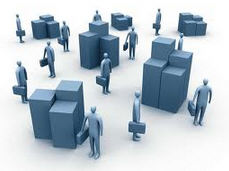 |
|
|
|
◆提高部門績效
◆提高員工生產力
◆提昇工廠管理績效
◆提昇組織學習能力
◆強化員工績效與薪資連結
◆組織架構與部門費用合理化 |
|
摘要: |
|
廠商為一設廠於中國大陸,大陸員工人數達萬人之大型鞋廠,為全球各大品牌代工製鞋。時當美國遭逢911事變,全球氣氛恐慌,品牌大廠訂單跟著急轉直下,企業主經營上面臨重大壓力與考驗。此時降低維運成本為當務之急,由於鞋廠為勞動密集之產業,在裁減管銷費用上最直接快速的方式是從現場生產部門著手,然而若未考量人員之績效、生產力、組織架構之調整等因素,而貿然裁撤部門與人員。當訂單回籠後,企業是否會因此失去反應能力和產能與品質上的優勢卻是更應該思考的問題。
在此組織再造合理化專案中,為降低員工人心浮動與對現有產能、生產力、品質最小之衝擊,裁取了漸近的方式來進行組織再造,先透過對組織架構、部門人員職能、績效、薪資結構的全面徹底調查,發現許多員工之薪資與其績效、管理幅度間存在不合理的現象。而製造現場亦有改善空間,而著手將現有人員配置與作業合理化進行改善;讓組織架構與部門費用合理化。一方面重新設計薪資結構,強化員工績效與薪資連結。 |
|
過程中,協助廠商建立改善小組,員工在專案進行過程中共同參與執行,使廠商藉此培訓管理人員與建立學習風氣,讓員工將所學習到之管理技術化為後續組織內部持續改善之動力。而在整個再造專案持續期間中,對組織所採取的人員精簡異動,並未引發演變成任何勞資上的重大衝突與爭議。
附記:此案之所以過程在勞資雙方之間並未有重大的衝突與爭議,原因之一也是在於企業主的氣度,企業主願意以員工的角度來思考,接納顧問建議要將企業目標與員工期待能趨於一致;將合理化精簡提昇效率後的成果,一部份與員工共同分享,顧問在此案中領會了一位優秀領導者的智慧。
|
|
|
|
|
|
|
|
|
|
|
|